Posts | Building Features | Structural Integrity
Pole Barn Columns: Laminated Posts vs Perma-Columns
Angie joined FBi Buildings in 2012 and is now the Director of Marketing. She's an avid reader and enjoys outdoor leisure and cheering on her two daughters at their sporting events.
As you enjoy your Sunday drive through the countryside, you can’t help but notice the diverse lineup of pole barns.
A sturdy farm shop for a hardworking farmer and his/her heavy machinery.
A spacious hobby barn for the classic car enthusiast and his/her collection.
An equestrian’s dream horse barn equipped with an indoor riding arena.
Indeed, the design flexibility of a post frame building is mind-boggling.
For a while now, you’ve been mulling around the idea of building a pole barn. It’s a big decision. After all, we’re talking about a large and rather permanent investment. At least, it should be permanent.
If you’re going to invest your money in a post frame building, you’ll need to make sure it’s engineered to handle various stresses. For example, your pole barn will encounter inclement weather (e.g., hail, rain, and wind). How your structure reacts to these inevitable situations will determine its lifetime.
Understanding the importance of your building’s structural integrity will help you:
- Make a well-informed buying decision
- Gain greater confidence and peace of mind
- Save money in the long run
Now, you’re probably wondering, “Where do I even begin?” We don’t expect you to be an expert in post frame construction. Each component of a building system is important. In this article, we discuss the structural difference between laminated columns and perma-columns.
What is Structural Integrity?
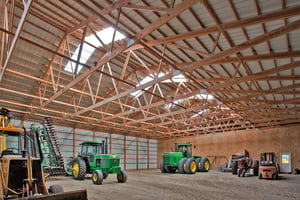
Structural integrity refers to a structure’s ability to withstand anticipated structural loads without breaking. Any building, regardless of size or location, must be designed to resist both vertical and lateral loads safely.
First, vertical loads act in the up-and-down direction. Examples of vertical loads include:
- Lofts
- Decks
- Second stories
- Snow
- Weight of the building itself
Second, lateral loads act in a direction parallel to the ground, such as strong winds and seismic activity (e.g., earthquakes). These forces can work in any direction. Therefore, the pole barn must be designed to withstand loads, both parallel and perpendicular to any wall.
All loads, both vertical and lateral, must be able to pass from the areas in which the load is applied. This transfer of forces through the structure is called the load path. A continuous load path carries all vertical and lateral loads from one building component to another until they reach the ground.
If the load path flows without interruptions, there will be no structural damage. However, one break in the path can cause damage. One “weak link” is all it takes to compromise the structural integrity of your pole barn. Therefore, each component must be strong enough to carry out these anticipated design loads.
What’s the Difference Between Laminated Columns and Perma-Columns?
Columns, also referred to as posts, are integral parts of a post frame building. They support the entire roof system and transfer all vertical loads to the footings. In addition, posts are the backbone of your walls and assist in resisting horizontal loads.
When selecting columns, do you know which types are offered? Let’s take a step back. Did you even know that you had a choice? That’s where post frame builders can help you out.
Most pole barn construction companies have a standard column option that they offer, as well as a durable upgrade.
Let’s look at it this way. You’re interested in purchasing a new vehicle, specifically a Chevrolet® Silverado. You can choose from several trim levels.
Do you want the basic LT model? Are you willing to pay more for the deluxe High Country edition? It boils down to personal preference. And that, our friend, is up to you.
As mentioned above, there are two types of columns: laminated and perma-column. Below, we compare the two popular options.
Laminated Columns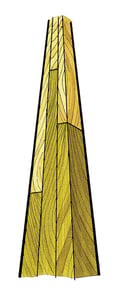
The term “laminated column” refers to two or more layers of dimensional lumber that has been mechanically laminated with nails. Typically, these posts are made from 2 x 6, 2 x 8, or 2 x 10 lumber. They’re strong, stress-rated, and pressure-treated.
Laminated columns are highly resistant to bending, twisting, or warping. Why? Because there’s very little chance of a knot being in the same place on all three pieces.
Not to mention, laminated columns have greater longevity than solid posts. Each layer of lumber is completely permeated with wood preservative and kiln-dried. This treatment prevents rot and termite damage.
For maximum protection, we recommend looking for columns that are saturated with more than 0.80 lb./cu. ft. of Chromated Copper Arsenate (CCA) wood preservative. That’s 33 percent more than industry standards, which you’ll find at hardware stores and lumberyards.
Next, your professional builder should set the columns at least 4’ below grade. This ensures:
- Adequate resistance to lateral and uplift forces
- No upheaval due to frozen ground in the winter months
The exception to this is if the column is anchored to a continuous concrete foundation.
Perma-Column® System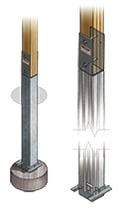
Alternatively, perma-columns are precast concrete columns that represent the evolution of post frame construction. They’re sized to fit any laminated columns or solid posts.
This sustainable solution is guaranteed to withstand insect damage, decay, and rotting. No wood goes into the ground.
Using 10,000 psi precast concrete, perma-columns are 3x stronger than standard concrete. Then, the columns are reinforced with 60,000 psi rebar welded to a ¼’’ steel bracket.
Furthermore, they include microfibers to add shock resistance and durability, and microsilica to enhance compressive strength and erosion resistance. A corrosion inhibitor protects the rebar reinforcement and brackets from rusting. A final admixture is added to give freeze and thaw protection.
Overall, this special mix guarantees a lifetime of durability. You’ll be avoiding thousands of dollars in repair costs (rotten wood) by upgrading to perma-columns.
Don’t Forget About the Foundation…
Selecting the right column for your pole barn is pointless if you’re not willing to invest in the proper foundation.
A foundation is the firm, solid basis by which columns are supported; a concrete footing for the column.
The building foundation must be able to support the intended structure and its design loads. It’s essential to the structural integrity and performance of your post frame building.
A long-lasting footer must meet the following criteria:
- Adequate size to support the intended structure
- Extend below exterior grade sufficiently to be free of frost action during the winter months
- Properly installed over well-compacted soil
- Consistent with the requirements of local building codes
Another factor to consider is the uplift anchor, which is located near the base of the embedded column. It significantly increases the force required to pull the column out of the ground.
Also, poured-in-place or precast concrete pads provide solid, non-shifting, load-bearing support. As a result, your pole barn won’t sink or get lifted out of the ground. If you opt for a continuous poured or block foundation, columns should be firmly anchored with special brackets.
Be sure your professional builder offers crushed rock (gravel) for backfilling column holes. This option provides the following benefits:
- More lateral and uplift resistance than backfilling with soil
- Less settling around the columns later (crucial for concrete floors)
Under no circumstances should pre-packaged, powdered concrete mix be used as the load-bearing basis for column holes. Powdered concrete requires ground moisture before it sets. Too little or too much moisture can cause weakening.
If your soil lacks sufficient moisture, the concrete will remain loose and unstable. Therefore, jeopardizing the structural integrity of your structure.
Which Column Will You Choose?
As one of the top post frame builders in the Midwest, it’s our job to get you thinking about your column options. Then, it's up to you to decide the right balance between strength and cost.
However, we strongly urge you to prioritize building longevity and strength over low initial cost. Remember the saying, “You get what you pay for?” Don’t forget it.
To read more about the other components that affect the building lifecycle, download our FREE Structural Integrity in Post Frame Construction guidebook. In the end, you’ll get the dream pole barn you’ve worked hard for and enjoy it for years to come.
Are you ready for a post frame building? You can design your own building with our new and improved online 3D design tool. Save, print, or email your final plan to family and friends.
Do you want a quote? Submit your design to us, and a member of our sales team will give you a call to begin the estimating process.
If you're ready to move forward with your post frame project, we also recommend you check out The Ultimate Guide to Building a Pole Barn. This guide will help you navigate the steps that you need to take to insure your project gets done on time and under budget.
Do you have more questions about pole barn columns that are not covered in this article? If you need help designing and planning, please contact FBi Buildings at 800.552.2981 or click here to email us. If you are ready to get a price, click here to request a quote and a member of our customer engagement team will help you determine the next steps of your project.