Posts | Building Features | Energy Efficiency
How are Post Frame Buildings Energy-Efficient?
Angie joined FBi Buildings in 2012 and is now the Director of Marketing. She's an avid reader and enjoys outdoor leisure and cheering on her two daughters at their sporting events.
When you hear the terms “pole barn or post frame building,” what image comes to mind?
- A durable farm shop for the hardworking farmer and his/her equipment?
- A large showroom exhibiting the newest sports car or heavy-duty truck?
- A spacious hobby shop for the classic car collector and his/her collection?
- A horse barn equipped with an indoor riding arena for the equine enthusiast?
- All of the above?
You can envision it now. A custom 56’ x 80’ x 14’ man cave/she shed featuring a deluxe kitchen for her social gatherings and storage room for his fishing boat.
However, there’s one particular concern that’ll influence your buying decision. How are you going to heat or cool your structure? It sounds expensive…
Not necessarily. Post frame bui-dings are more energy-efficient than the following materials:
- Concrete blocks
- Stud wall
- Steel framing
To a building owner, energy is the largest controllable operating expense. In this article, we examine the advantages and basic components of an energy-efficient pole barn.
3 Advantages of an Energy-Efficient Pole Barn
Globally, code officials recognize the need for a modern, up-to-date energy conservation code (ECC) addressing the design of energy-efficient building envelopes and related systems.
Some U.S. states have adopted ECC and require HVAC buildings to be code-compliant. Please contact your city hall or county courthouse for minimum design and construction requirements. You may wish to follow the guidelines, even if it’s not required in your area.
Below, we discuss the three benefits of having an energy-efficient pole barn.
1) Good for Your Budget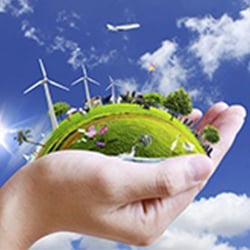
Are you interested in reducing your utility costs? If you answered “yes,” then an energy-efficient design is your best hedge against escalating prices. A post-frame building can minimize energy consumption and help you realize tangible savings.
While there may be some initial costs, the energy-saving components will in turn provide cost savings, resulting in long-term lower utility bills.
Plus, in the United States there are sometimes en,ergy tax rebates on items, such as windows.
2) Good for the Environment
Carbon footprint is a major societal conversation. Not only does an energy-efficient building deliver economic gain, but it provides broader environmental benefits.
It’s not rocket science. Lowering energy use increases the air quality improves air quality, allocates resources more efficiently, and reduces
3) Good for the People (and Animals) Using It
Energy efficiency isn’t just about saving money or being environmentally conscious. At the end of the day, it’s about making your pole barn a comfortable space to:
- Work on your machinery (e.g., tractor or combine)
- Sell your products or services to consumers
- Spend quality time with family and friends
- Groom, house, and ride your horses
Your post frame structure should meet your needs (and expectations). Monetary and environmental savings are a bonus.
Determining the Cost of an Energy-Efficient Pole Barn
Now, you’re probably thinking, “Those advantages are all well and good, but energy efficiency sounds expensive.” It boils down to perspective.
Generally, the more energy-efficient choices you make for your pole barn, the higher the up-front investment.
However, those additional expenses can be offset by lower operating costs. To determine which upgrades will provide a good return, you’ll need to:
- Establish a baseline building
- Compare that to an upgraded building in terms of cost and performance
It may sound intimidating. Knowledgeable sales consultants and in-house engineers can walk you through variables and arrive at the best decision.
Designing and Construction for Energy Efficiency
Before you plan a climate-controlled space, you need to understand the importance of the building envelope.
What is the Building Envelope?
First, the building envelope (or shell) consists of materials that separate the outside from the inside. These components include the roof, attic, walls, foundation, doors, and windows.
How does it affect energy efficiency? The building design determines the amount of energy a pole barn will use.
What is Heat Transfer?
Naturally, heat flows from warm to cooler spaces until the temperatures equalize. It travels in one of three ways, through:
- Conduction
- Convection
- Radiation
A well-designed building envelope will reduce all three types of heat transfer.
Conduction
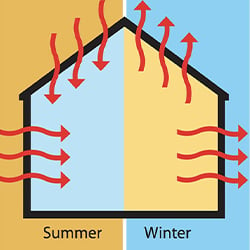
Conduction is the term applied to heat flow within a solid material. You can reduce conduction heat loss by using building envelope materials with high R-values.
A rating known as an R-value measures a material's resistance to heat flow. The higher the R-value, the higher the resistance to heat loss.
Furthermore, the amount of R-value your pole barn will require depends on the following factors:
- Climate
- Type of heating and cooling system installed
- Area size needing that extra layer of defense
Although this is a useful measure, it is only one way to gauge effectiveness. Therefore, the entire “system” must be considered.
Convection
Convection is the process of transferring heat from one place to another through gas or liquid.
This type of heat loss occurs when warm air escapes and cold air enters. You can reduce it by limiting the amount of air infiltration and exfiltration through the building envelope.
Radiation
Radiation is heat transfer by electromagnetic waves from a warmer to cooler surface. The transfer of the sun’s heat to earth is a prime example of radiation.
Why Do These Components Need to Work Together?
Each building material is a pathway for heat transfer. These components work together to control the energy flow between the interior and exterior.
So, what are the building components that impact energy use? Let us explain.
4 Building Envelope Components that Impact Energy Use
The following components will help lower heat conduction, maximize comfort, and minimize fuel bills. Who could say no to that?
1) Insulation
Insulation is the primary defense against heat loss through the building envelope. Only climate-controlled spaces should be well-insulated.
After you select a heating system, you’ll need proper insulation to maintain a warm temperature. There are several types of insulation materials, so the choice is yours.
Perimeter Slab Insulation
If you go outside to your garage, chances are it has a concrete slab floor sitting on top of the ground. Moreover, the ground has its own R-value. So, if you insulate around the perimeter, you can protect that R-value and prevent heat from escaping around the building.
Typically, a dense 2-inch rigid board insulation is vertically installed alongside the columns, or horizontally under the floor.
Does your pole barn have in-floor heating? Or maybe it sits over a high water table? If so, you’ll want to insulate under the entire floor. Otherwise, the water will steal the heat as it flows away from your building.
Wall Insulation
The walls of your post frame building act as barriers from the harsh winter weather. Without wall insulation, conduction will occur regardless of the heating-cooling system you have employed. That’s a waste of your hard-earned money!
For instance, heat will exit your tool shed even if the furnace is running full steam ahead. Therefore, adding insulation will significantly reduce heat conduction.
Below are five types of wall insulation used in pole buildings:
Fiberglass Batts
First, fiberglass batts are the most common insulation in the walls of post frame structures. It’s well-known for its relatively low cost and ease of installation.
Long spans of fiberglass insulation can be placed in-between posts, resulting in fewer breaks (air leaks) between batts.
If you choose fiberglass batts, you’ll want to look into a vapor barrier. It’s an impermeable material placed in-between the interior wall and insulation.
Vapor barriers minimize condensation caused by moisture build-up within the envelope. This helps prevent insulation from getting wet, which lessens its performance and contributes to its deterioration.
Vinyl Back
On the other hand, a vinyl back is a fiberglass batt with a white coating. Usually, it’s fitted in-between framing, but that can cause issues with sagging. Also, it can be a challenge to install properly. The R-value varies by thickness.
Sprayed Polyurethane Foam (SPF)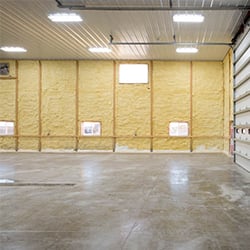
In recent years, sprayed polyurethane foam (SPF) has become a popular but expensive alternative to fiberglass batts. SPF fills and seals all exposed areas and cracks within the building, giving you greater protection from air drafts and moisture.
Due to the chemicals and equipment involved, a professional spray-foam contractor should be hired to do the job.
If part of your wall needs to be replaced at any given point, this type of material can be challenging to remove due to its glue-like characteristics.
On top of that, some spray foam products haven’t been tested for steel use. Consequently, some metal suppliers won’t provide warranty coverage if SPF is used. Check with your professional builder before making a final decision.
Rigid Board Insulation
Installed directly underneath the exterior steel siding, these rigid panels of insulation provide a very high R-value with continuous coverage. As a result, there is less air infiltration.
Note: Not all rigid board products are created equal. Please make sure it is approved for use in exposed applications.
Building Wrap
Although it isn’t considered a type of insulation, building wrap is an optional barrier. Similar to the rigid board, it’s installed underneath the exterior siding of your pole barn.
Also, building wrap is an additional moisture and air infiltration barrier. It works together with your insulation to keep your interior comfortable.
Before purchasing, please consider building codes, siding, and insulation type to determine if building wrap is a wise investment for you.
Attic Insulation
In post frame buildings, fiberglass batts and blown insulation are most frequently used for attics.
When properly installed, the attic insulation provides an airtight finish between the ceiling joists and bottom chords of the trusses.
A contractor with specialized equipment applies blown insulation. It’s easy to install (no need to cut and fit) and can adapt to any R-value.
According to the North American Insulation Manufacturers Association (NAIMA), most energy codes recommend anywhere from R-30 to R-49 for attics. Again, your professional builder should know the code for your area.
Not to mention, blown insulation conforms to small and odd-shaped spaces.
Roof Insulation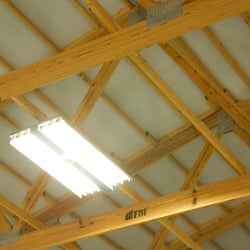
Lastly, an insulated roof is a lower-cost alternative to a complete liner package with attic insulation. Typically, it is installed under the roof sheathing, exposing truss members.
This type of material works well with radiant heat as opposed to forced air. With the latter, much of your heat rises into the truss space.
Rigid board insulation, such as Thermax®, is a common roof application. It prevents the need for other interior finishes (e.g., drywall).
A radiant barrier (the combination of batts and spray foam) resists heat flow by absorbing and slowing down the heat transfer. Then, it plugs any air leaks.
Radiant barriers can be placed anywhere in your building. But, it works better in attics or under roofs of air-conditioned buildings.
Note: a radiant barrier will only work when at least one side is facing an air space.
2) Attic Ventilation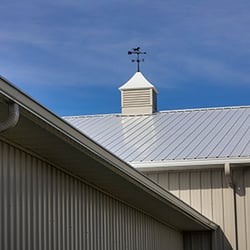
Do you plan on having an attic above your pole barn? If so, proper attic ventilation plays a critical role in the building envelope.
Ventilation is the intentional exchange of indoor air with outdoor air. The primary purpose of pole barn ventilation is to prevent condensation (moisture build-up).
Condensation occurs when warm, moisture-laden air contacts a cooler surface, such as the underside of your roof steel. Since lower-temperature air cannot hold as much moisture as warmer air, the excess humidity turns into water droplets. Then...drip, drip, drip!
With any structure, moisture can cause the following damage:
- Mold growth
- Material decay
- Poor human/animal health
- Discoloring of equipment and furniture
As a result, ventilation works to minimize the temperature difference between indoor and outdoor air. How so? By drawing in fresh air and exhausting stale air.
Attic ventilation can be accomplished passively or actively through natural and mechanical distribution, respectively.
Natural Ventilation
Uncontrolled air movement into the attic through vents. The proper location of these openings is of primary importance in obtaining natural ventilation.
Mechanical Ventilation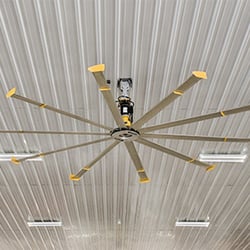
Opposite of natural ventilation, mechanical ventilation controls the air movement by using one or more fans. It isn’t commonly used for post frame buildings because it increases initial, operating, and maintenance costs.
Mechanical ventilation is used when natural ventilation isn’t enough. In this case, you’ll want to consider installing the following interior items:
- Ceiling fans
- Portable fans
- Larger, installed fan units
- Or a combination of any listed above
However, we recommend passive ventilation compared to active from a cost-effective perspective.
3) Roofing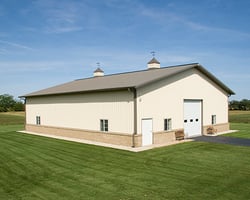
Next, the new and improved “cool metal roofing” is becoming a popular feature of post frame buildings.
A cool metal roof has a high solar reflectance and high thermal emittance. The emittance of a material refers to its ability to release absorbed heat.
Generally, lighter colors perform better. But, darker colors can perform well with special paint coatings.
A roof with high solar reflectance has a lower surface temperature compared to one with low reflectance. If the roof has high emittance, the little heat it absorbs is released quickly.
Overall, this translates into less heat gain inside the building envelope, resulting in a cooler interior.
4) Doors and Windows
Lastly, doors and windows not only create views but admit energy and supply natural ventilation. The form, size, and location of these openings vary depending on the building envelope.
A great deal of heat loss will occur around these components. Therefore, selecting the right quality (and quantity) of doors and windows will be a major decision. There are several energy efficient window options for pole barns.
Be sure to hire a contractor who makes precise installation a priority.
Are You Ready to Get Started?
Whether your goal is to save money or to impact the environment positively, having an energy-efficient pole barn is a smart move. Energy conserved is money saved.
For more information, you can download our FREE Energy Efficiency in Post Frame Construction guidebook. With our expertise, you’ll discover how to reduce utility costs and enjoy the money-saving benefits.
Have more questions about energy efficiency not covered in this article? Please contact FBi Buildings at 1.800.552.2981 or click here to email us. If you’re ready to get a price, click here to request a quote and a member of our sales team will call you.