Building Construction | Posts | Site Preparation | Building Design
3 Types of Pole Barn Foundation: Which One is Best for You?
Cori grew up on her family's small grain and livestock operation in Northwest Indiana. In 2018, she graduated Summa Cum Laude with a Bachelor's degree in Business Administration & Marketing from Marian University Indianapolis. Having shown beef cattle for 12 years at the county, state, and national levels, Cori chose to pursue a career in agriculture. Today, she serves as the Marketing Content Creator on the FBi team. In her free time, Cori enjoys spending time with family and friends, watching sports, listening to live music, and traveling.
Every post-frame building must sit upon a solid foundation. This firm basis, along with properly installed footings, supports the entire pole barn and its design loads. A weak foundation can put the structural integrity of your post-frame building at risk.
To help you avoid structural failure and subsequent stress, we’ve detailed the three types of pole barn foundations for your post-frame project.
Don’t have time to read this article? Watch the video below for an in-depth look at the pole barn foundation options offered by FBi Buildings.
3 Types of Pole Barn Foundation: Which One is Best for You?
1) Pre-Cast Pad Foundation
First, pre-cast concrete pads provide non-shifting and load-bearing support, so your post-frame building doesn’t sink or uplift from high winds.
The embedded column is attached to an uplift anchor, significantly increasing the force required to pull it out of the ground.
According to Midwest Perma-Columns®, their concrete pad options exceed industry standards for strength and are unreinforced.
Note: The pole barn foundation must be evaluated with respect to the soil cone. Please consult with your post-frame engineering team for proper sizing.
- Pros: No concrete needed (cheap and fast installation)
- Cons: Wood in the ground (shorter lifecycle)
2) Poured-in-Place Foundation
Next, a poured-in-place concrete foundation consists of wooden forms on top of the footings. This pole barn foundation is popular with residential buildings.
The wooden forms, or molds, shape the walls of your pole barn foundation. They’re also built around steel rebar, which adds additional strength.
Then, concrete is poured into the wooden forms. Once the mixture cures, the molds are removed, leaving you with a poured-in-place foundation.
Columns must be firmly attached to the foundation with brackets designed for this purpose. As a result, no wood goes into the ground, which prevents rotting columns.
However, a poured-in-place foundation is more expensive due to the contractors needed and equipment used.
- Pros: Higher quality foundation than pre-cast pads
- Cons: Expensive, concrete can break down over time
3) Continuous Poured Foundation
Lastly, a continuous poured foundation consists of a concrete wall extending above the footings.
This pole barn foundation is commonly used for complex buildings, such as commercial businesses. They achieve maximum effectiveness in bedrock and sand conditions.
Like poured-in-place foundations, the columns must be attached to the continuously poured foundation with special brackets.
- Pros: Strong basis, greater longevity, the best option for insulation
- Cons: Expensive
Other Factors to Consider When Selecting a Pole Barn Foundation
Below, we detail three factors you should consider when selecting a pole barn foundation. These features will set your post-frame building up for success.
1. Laminated Posts or Perma-Columns
In pole barn construction, there are two types of columns: laminated posts and Perma-Columns.
The term “laminated post” refers to 2+ layers of dimensional lumber that has been mechanically laminated with nails.
These columns are typically made from 2x6, 2x8, or 2x10 lumber. They’re strong, stress-rated, and pressure-treated.
Laminated posts resist bending, twisting, and warping because there’s very little chance of a knot being in the same place on all three pieces.
Not to mention, they have greater longevity than solid columns. Each layer of lumber is completely permeated with wood preservative and kiln-dried. This treatment prevents rot and termite damage.
Moreover, your post-frame builder should set the columns at least 4’ below grade. This placement ensures:
- Adequate resistance to uplifting forces
- No upheaval due to frozen ground during the winter months
Note: The exception is columns anchored to a continuously poured foundation.
Alternatively, Perma-Columns are pre-cast concrete columns that fit any laminated or solid post. This sustainable solution is guaranteed to withstand any insect damage or decay because no wood goes into the ground.
Using 10,000 PSI pre-cast concrete, Perma-Columns are three times stronger than standard concrete. Then, the columns are reinforced with 60,000 PSI rebar welded to a ¼’’ steel bracket.
Furthermore, Perma-Columns include microfibers to add shock resistance and durability. Microsilica enhances compressive strength and erosion resistance. A corrosion inhibitor protects the rebar and brackets from rusting.
Overall, this mixture guarantees a lifetime of durability. By upgrading to Perma-Columns, you’ll avoid thousands of dollars in repair costs.
Note: This option is only available with pre-cast and poured-in-place foundations.
2. Gravel Backfill
When backfilling the column holes in your pole barn foundation, we highly recommend using crushed rock (gravel). This option provides the following benefits:
- More resistance to uplifting forces than backfilling with soil
- Less settling around the columns (crucial for concrete floors)
Under no circumstances should pre-packaged, powdered concrete mix be used as the load-bearing basis for post holes.
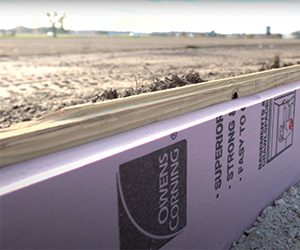
Powdered concrete mix requires ground moisture before it sets. Too little or too much moisture can cause structural integrity issues.
3. Rigid Board Insulation
Last but not least, rigid board insulation may be required for your post-frame project, especially for commercial buildings (per codes).
These foam panels are bracketed to the baseboards. They’re energy-efficient and keep your pole barn cool in the summer and warm in the winter.
Which Pole Barn Foundation Will You Choose?
Now that you’ve read through the pole barn foundation options (or watch our YouTube video), have you decided which one you’ll choose?
If you need more guidance, our Project Sales Consultants (PSCs) can walk you through the building process and answer any lingering questions.
We also recommend downloading our “Structural Integrity in Post-Frame Construction” guidebook. This FREE resource explains how each building component, including the foundation, plays a vital role in pole barn structural integrity.
Have more questions about pole barn foundations that aren’t covered in this article? Please contact FBi Buildings at 1.800.552.2981 or click here to email us. If you’re ready to get a price, click here to request a quote, and a member of our sales team will call you.