Posts | Building Tips | Comparisons
FBi Buildings vs Morton: Who's Best for Your Project?
Angie joined FBi Buildings in 2012 and is now the Director of Marketing. She's an avid reader and enjoys outdoor leisure and cheering on her two daughters at their sporting events.
Our builder comparison for this week is featuring Morton Buildings.®
Arguably one of FBi’s biggest competitors, Morton constructs post-frame buildings for ag, commercial, residential, community and equine facilities. They’re firmly committed to being the industry leader, focusing on innovation, service, and quality.
Morton pledges to construct only high-quality, post-frame structures that help make your dreams come true.
In this blog, we will be presenting the facts and strengths of each builder. Our goal is to help you better understand how FBi compares to Morton before you make a final decision.
FBi Buildings vs Morton: 7 Key Differences to Look For
1. Customer Service
FBi Buildings
From the first call into the office all the way to the last call with your Project Manager, FBi tries to ensure that you’re aware of what’s going on with your post-frame building project every step of the way.
Each customer is assigned their own personal Project Sales Consultant who lives in their area. FBi currently has 30+ Project Sales Consultants spread throughout our service area, covering designated territories. This allows them to meet with you not only to understand your needs in person but also to walk your property and help you identify the best location for your building.
Once the project is finalized and you’re ready for construction, you will be given a personal Project Manager. They are responsible for scheduling FBi’s crews and providing resources to help check your site prep or answer other questions you might have.
FBi’s Project Managers help outline your project in four specific phases:
- Processing: This is an overview of the first steps of your construction project. This is also where FBi will be going over site preparation, permitting, and approximate start time.
- Design & Permit: FBi will follow up with you about your building permits and site prep updates. Your Project Manager will also review your construction drawings and validate the expected construction start date.
- Pre-Mobilization: Involves your Project Manager in completing the steps to set the date the crew and material will arrive.
- Construction: This phase details the main milestones that will happen during construction that you need to be aware of along with the finishing steps after completion.
Morton Buildings
Morton’s customer service approach is slightly different from FBi’s. Instead of having a designated Project Sales Consultant and Project Manager you will only have one point of contact throughout the entire construction process. Your Morton Sales Consultant will also be responsible for scheduling the construction of your building as well as the delivery of your materials and any other services that might be needed (dumpster rental, porta potty, etc).
Who has the best customer service?
Both companies offer assistance every step of the way, but with different approaches. Having one point of contact with Morton from start to finish can help reduce change and be a value add upfront. FBi’s approach of switching from your Project Sales Consultant to your Project Manager can be a negative change at first when compared to Morton’s consistency.
However, FBi’s Project Managers are able to spend all their time on sold contracts and assisting you through your entire construction process. In contrast, Morton’s sales representatives are still tasked with selling other projects and can be harder to get ahold of due to their multiple roles.
2. Service Areas
FBi Buildings
FBi is a family-owned company that started in 1958. Their corporate headquarters is located in Remington, Indiana. During that time they’ve been known as the preferred pole barn builder in the Midwest.
Currently, their service area is limited to Indiana, Illinois, Iowa, Michigan, Ohio, Wisconsin, Missouri, Tennessee, and Kentucky. However, if you have a unique project that is outside of their building territory, they will look into pursuing other options to see if it is feasible for them to be your pole barn builder.
Morton Buildings
Founded in 1903 as the Interlocking Fence Company, Morton’s core function was to sell fencing by mail to farmers. In 1949, they created their first machine storage building for farm use. By 1964, what was once known as the Interlocking Fence Company became Morton Buildings.
With their headquarters located in Morton, Illinois, Morton operates over 100 employee-owned construction centers and have offices located in over 30 states.
Who has the best service area?
Morton easily wins this area. With seven manufacturing plants and their service area coverage across 30 states can’t be beaten.
3. Pole Barn Materials
Steel
FBi Buildings
FBi’s panels are 29 gauge, heat-treated, full-hard, high-tensile steel with a minimum yield point of 80,000 PSI (pounds per square inch). That’s 60 - 78% higher than what’s commonly used.
A high yield is nearly twice as strong as other steel and can improve the structural integrity of your building by providing greater resistance to impact damage from hail, rocks, etc.
Their buildings also feature galvalume walls and roofs. Depending on what pole barn color you choose, FBi will also use galvanized steel panels on their walls.
Galvalume combines aluminum, silicon, and zinc coating to fight corrosion. This is different from galvanized steel, where corrosion will begin to spread once the galvanized coatings wear down or are penetrated.
Morton Buildings
Unlike FBi, Morton uses 26-gauge commercial quality Hi-Rib™ steel manufactured at their plant.
Morton’s panels have rib heights up to 33% higher and steel thickness up to 25% thicker than panels used by other builders. Morton uses two different types of coating (zinc or a mixture of zinc and aluminum) to protect their steel.
Galvanized steel is 100% zinc, while Galvalume is 30% zinc and 70% aluminum.
Flat sheets of steel are run through a roll-forming machine to get the strength needed to carry roof loads. To form the ribs, the steel is stretched and bent.
Who has the best steel?
There’s a lot of back and forth between builders on the importance of steel strength and what type of steel gauge you should use for your post-frame building. However, we have to give Morton a nod for manufacturing their own steel and offering stronger steel.
When comparing the two metals, FBi’s steel has a higher yield strength (80,000 PSI) than Morton's (40,000 PSI). This rigid material will better withstand projectile damage (e.g., hail and rocks).
Watch the video below to see how FBi and Morton’s steel compares when put under the typical pressure of a post frame building.
Wood
FBi Buildings
The type of wood that FBi uses is dependent on the building design. For example, if you’re going to build a pole barn that will have large clear spans than FBi will use Machine Stress-Rated (MSR) lumber for their trusses. Each piece of MSR lumber is tested for stiffness and strength prior to being used.
FBi will also use #1 lumber for jobs that require smaller trusses.
Morton Buildings
Morton’s wood selection process is identical to FBi’s. They also use MSR lumber that is tested for stiffness and strength prior to being used on any job.
Who has the best wood?
Both companies are equal when it comes to the type of wood being used. Therefore, this section is a tie between FBi and Morton.
Screws
FBi Buildings
FBi uses a stainless steel capped, self-sealing screw. The screw fasteners encapsulate the sealing washer to protect it from the elements and to improve aesthetics.
The washer maintains its seal and is more reliable than commonly used neoprene, and offers the best heat, cold, weather, and ozone resistance.
Morton Buildings
Morton developed their own stainless steel screw - the Stainless Steel Internal Drive® Screw.
This screw was created to provide a color-matched fastener that would look better and virtually eliminate the possibility of rust. This fastener features a solid stainless steel head and shank, as well as a separate stainless steel and EPDM washer. The screw also revolves independently to reduce damage caused by metal shards during installation.
Who has the best screws?
Morton gets a nod for developing their own screws, but the winner of this category goes to FBi. FBi is the better choice for screws because the screws that they use are stainless steel. The head of the screw is formed to “umbrella” the washer to protect it from the elements and dry rot, longer. If you are worried about roof leaks, you’ll want to make sure that you have a screw that is protecting the water sealing washer. FBi’s stainless steel head is guaranteed to never rust.
Morton’s hex head is flat and there’s no UV protection for their washer. Their shank of the screw is also softer because it’s full stainless steel. This also makes it a prime candidate for rust.
Trusses
FBi Buildings
FBi trusses are made in their own plant and engineered specifically for your building. Their truss plant is also certified by a third party Truss Plate Institute inspection service to ensure the quality fabrication of all trusses.
The lumber used to build the trusses is joined with heavy-duty steel plates. These plates have a dense concentration of long teeth providing excellent grip on the wood.
Morton Buildings
Similar to FBi, Morton also builds their trusses in-house. Each truss is built specifically for the type of building, meaning no two trusses are built the same.
Morton’s specially engineered trusses are made from premium-grade lumber. For added strength and corrosion protection, the factory fabricated trusses include heavy-duty zinc galvanized gusset plates that are rolled on during construction. The predrilled, factory-cut continuous purlin system adds strength, rigidity, and uniformity.
Who has the best trusses?
FBi wins this narrowly as they press their steel plates on their trusses instead of rolling them on. Using this technique allows FBi to be even more precise when engineering truss strength when compared to Morton rolling their truss plates on.
Paint
FBi Buildings
FBi’s side and roof panels are finished with the Kynar 500 Fluoropolymer paint system. This system isn’t just a wet dipped or sprayed on paint, it’s baked on paint that has a strong resistance to fading, chalking, and corrosion.
Developed in the 1960s, Kynar was initially produced by a single manufacturer for use on historic and monumental buildings. Their panels are known to retain their rich color for 40 years or longer.
Morton Buildings
Morton offers the FLUOROFLEX® paint system. FLUOROFLEX 1000 consists of a 70% polyvinylidene difluoride (PVDF) topcoat or “color coat” and polyurethane primer that is coated onto a heavy GALVALUME® or a heavy hot-dipped galvanized steel substrate.
Their panels are known to be virtually maintenance-free, easy to clean, and will maintain their rich color for 35 years or longer.
Who has the best paint?
Both paint systems are extremely well known in the post frame industry, and have a strong resistance to fading, chalking, and corrosion. This one is a tie between FBi and Morton.
Columns
FBi Buildings
There are two types of ground contact for your columns that you can choose from when pricing your building: Laminated and Perma-Column.
Similar to FBi’s trusses, they also build their laminated columns in-house. Laminated columns have greater strength in standard post frame buildings and longevity against rot than solid posts. Each layer of ground contact lumber is completely permeated with wood preservative and kiln-dried.
Not all column treatments are equal. FBi uses a .80 treatment in their columns which is 33% greater than industry standards. This treatment prevents rot and termite damage.
Alternatively, you can use Perma-Columns which are precast concrete columns. This sustainable solution is guaranteed to withstand insect damage, decay, and rotting as no wood goes into the ground.
Using 10,000 PSI precast concrete, perma-columns are 3x stronger than standard concrete. Then, the columns are reinforced with 60,000 psi rebar welded to a ¼’’ steel bracket.
Morton Buildings
Morton believes that you can extend the life of your post frame building by using concrete lower columns in your foundation, rather than wood. By removing wood from the ground, they believe you’ll get a stronger, more durable building.
They call this evolution the Morton Foundation System™ (MFS). All Morton buildings come standard with this system.
They key benefits of the MFS are:
- Removes wood from the ground
- No need for treatment, providing an eco-friendly option
- Their pre-form concrete column strength is 2.5 times greater than a typical concrete foundation wall
- 50-year warranty
- Increased durability to corrosion, shock, freeze and thaw cycles
Who has the best columns?
Morton comes out on top with this one. Both companies offer a concrete column option that are known to last longer than any laminated column. However, the difference is FBi’s Perma-Column is an upgrade and Morton’s MFS comes standard with their buildings.
Doors
FBi Buildings
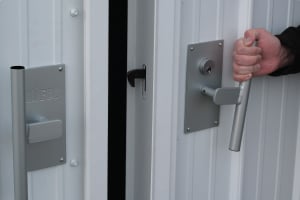
Sliding Doors
FBi’s EasyMotion sliding door was introduced in 2010. One of the perks that’s included with this door is the StepSaver Latch. This system saves you time and energy.
No more running around to the walk-in door to disengage cam latches and snugger chains. Just turn the key and grab the handle. It’s that simple!
The EasyMotion door also features the Posi-Guide Track. This guide doesn’t collect rain, ice, snow, or debris (i.e., bird nests and leaves). A unique low-friction polymer roller is protected behind and underneath the track. This system keeps the door snug to the building as it operates.
Overhead Doors
Overhead doors are something that is not standard with FBi’s buildings. If you’re interested in having overhead doors on your building we will work directly with our preferred vendors to supply you with the style and size needed.
FBi’s in-house engineers carefully evaluate the entire building system and will specify the necessary foundation, column and header sizes to carry the expected loads for each door.
Morton Buildings
Sliding Doors
Similar to FBi, Morton also has their own sliding door system. They call this system the AlumaSteel® Sliding Door System. This door system also includes an exterior opening system similar to StepSaver.
Their sliding doors open and close easily and are warranted for five years with no wind velocity limit. They’re also color-matched to accent your building and are available in a variety of widths (from 8’ to 40’).
Overhead Doors
Similar to FBi, overhead doors are something that does not come standard with Morton buildings. If you’re interested in having overhead doors on your building they will also work directly with their preferred vendors to supply you with the style and size needed.
Who has the best doors?
Where FBi separates themselves from Morton is their posi-guide track. FBi’s track being off the ground helps eliminate rocks, sticks, or leaves from jamming the door and needing to be cleaned.
However, if you prefer to use overhead doors then both companies are capable of finding preferred vendors to work with.
Windows
FBi Buildings
Believe it or not, there’s a lot of decisions to make when choosing windows for your pole barn. The windows that we offer are energy-efficient and come in popular styles.
Some of your choices could include the following:
- Double-hung
- Single slider
- Eyebrow
- Half-round
- Gothic
- Full Circle
- Hexagon
- Quarter-round
Morton Buildings
Morton also offers a wide variety of energy-efficient windows that come in several popular styles. Whether you’re looking for windows with grids, windows with shutters, or horizontal sliding windows...you’ll be able to choose from a variety of sizes.
Who has the best windows?
This is a tie between FBi and Morton as they both offer windows with their buildings. We do offer one piece of advice though...don’t be afraid to shop around. Sometimes you’ll find similar windows for a cheaper price at your local hardware store.
Who has the best materials overall?
Out of the eight different material categories FBi comes out the winner. They win five out of the eight categories; those being steel, screws, trusses, doors and paint. Morton ties FBi with their wood, columns, and windows.
4. Delivery
FBi Buildings
The same day that your construction starts, your material will be delivered on-site. FBi doesn’t prefer to deliver your materials to your site and have them sit out in the elements until the crew shows up. Depending on the size of your project will also determine the size and type of equipment that will be showing up.
FBi normally brings the following equipment to a job-site:
- A semi for material and delivery
- Gradall / telehandler
- Crew truck and trailer
- Skid-steer. if applicable
- And a crane, if applicable
Their materials are delivered with company employed drivers straight from their own lumber yard.
Morton Buildings
Morton’s delivery approach is slightly different from FBi’s. Yes, they do have their own delivery trucks and personal drivers, but they do not direct ship their materials in conjunction with their construction crews showing up.
Their salesman schedules when the material will be shipped and the driver stages it when he arrives on site. This could be a con because the crew foreman isn’t there to help the driver stage the material and the material could be on site longer than what it needs to be.
Who has the best delivery?
Morton gets a nod for their wider range of delivery service, but the winner here is FBi. FBi takes this one due to a more personalized and comprehensive approach to delivery that is in conjunction with their crews showing up onsite.
5. Construction
FBi Buildings
The quality of the construction crew is a major factor in building your pole barn. Experienced men make fewer mistakes, giving you a higher quality building.
FBi Buildings crews are employees of FBi Buildings and are specifically trained in the safe construction of pole barns. FBi buildings strive to employ local individuals for crews across their expanding territory. This allows their 45+ crews to serve an area they are familiar with.
FBi Building's commitment is to provide you with excellent service from start to finish! We have a Crew Management team of construction veterans who oversee and support the foremen and his crew. In fact, our average tenure is over 17 years between our foremen and our crew management team!
Morton Buildings
Morton also employees their own construction crews, and their crew foreman are provided with continuous education on safety, quality, and productivity. On average, their crew foreman have 16 years of experience.
Similar to FBi, they also have their training program called Morton 36.
Who has the best construction?
Both companies provide experienced construction crews, therefore this section is a tie. Between the continuous training courses and the experienced Construction Management teams, your building is in good hands if you choose FBi or Morton.
6. Warranty
FBi Buildings
A pole barn warranty is simply a promise to stand behind a product or service. All warranties are limited, and there is no standard warranty in the post frame industry.
Here’s what’s covered under FBi’s warranty:
- Columns: Lifetime
- Roof Structure: 20 Years
- Red Rust: 15 Years
- Paint: 40 Years
- Gloss Loss: 5 Years
- Roof Leaks: 5 Years
- Sliding Doors: Lifetime
- Workmanship: 1 Year
Morton Buildings
Morton also offers a warranty on their pole barns. As mentioned above, there is no standard warranty in the post frame industry so when you’re comparing builders it’s important to ask for the builder’s warranty before making a final decision.
Here’s what’s covered under Morton’s warranty:
- Columns: 50 Years
- Roof Structure: 50 Years
- Red Rust: 20 Years
- Paint: 35 Years
- Roof Leaks: 5 Years
- Sliding Doors: 5 Years
- Workmanship: 1 Year
Who has the best warranty?
FBi wins this with having a more comprehensive list of warrantied features and their coverage is longer lasting on average.
7. Cost
FBi Buildings
FBi is well aware that they aren’t the cheapest post frame builder out there, but they also aren’t the most expensive.
A standard pole building shell can cost anywhere from $20 to $60 per square foot. Now, you’re probably asking yourself, “Why is there a big difference in price per square foot?”
Here’s why...
The following factors will determine if your pole barn is leaning towards the low/high side of the cost spectrum:
- Total square feet
- Type of features (e.g., overhangs, windows, walk-in doors, steel liner packages, etc.)
- Current nature of the commodities market (the price of steel)
For example, adding a porch, cupolas, and numerous doors will push you closer to the $45 per square foot depending on the size of the building.
Morton Buildings
Similar to FBi, there is no concrete cost when it comes to pricing a Morton building. A variety of factors will influence the cost of your pole barn. Those factors are:
- Building size
- Building location
- Building site
- Building features
- Scope of work
For example, a 42’ x 64'’ x 10’-4" garage with 2 overhead doors, overhang, walk door, wainscot, and no insulation would cost $30/square feet.
However, a 24’ x 32’ x 10’-4" building with the same features would cost $55/square feet.
Who has the best cost?
When removing all factors that go into cost and just look at the raw cost between the two companies FBi will typically win this battle.
Who’s Best for Your Post Frame Building Project?
NOTE: The star denotes personal preference based on the buyer. Please reference each section for specifics.
Every builder has their advantages and disadvantages, and the final decision is solely up to you and your specific needs.
- Morton is the way to go if you’re looking for a national builder and would prefer to have one point of contact throughout the entire construction process.
- FBi Buildings is the right choice if you’re looking to make a long-lasting investment and would like to get a more personalized sales experience.
If you’re still unsure about what to do, we recommend checking out these additional resources:
- FBi Buildings vs Menards: Who’s Best for Your Project?
- FBi Buildings vs Cleary: Who’s Best for Your Project?
- 7 Questions to Ask Your Pole Barn Builder
- Pole Building Prices: 6 Considerations for Comparing
- What is Site Preparation? 7 Tips to Get You Started
We’d be happy to work with you on your pole barn project if you’re located in Indiana, Illinois, Iowa, Kentucky, Michigan, Missouri, Ohio, or Wisconsin.
Do you have more questions that are not covered in this article? If you need help designing and planning, please contact FBi Buildings at 800.552.2981 or click here to email us. If you are ready to get a price, click here to request a quote and a member of our customer engagement team will help you determine the next steps of your project