Pole Barn Structural Integrity: Top 5 Building Components
Cori grew up on her family's small grain and livestock operation in Northwest Indiana. In 2018, she graduated Summa Cum Laude with a Bachelor's degree in Business Administration & Marketing from Marian University Indianapolis. Having shown beef cattle for 12 years at the county, state, and national levels, Cori chose to pursue a career in agriculture. Today, she serves as the Marketing Content Creator on the FBi team. In her free time, Cori enjoys spending time with family and friends, watching sports, listening to live music, and traveling.
As you enjoy your Sunday drive through the countryside, you can’t help but notice the diverse lineup of pole barns.
The durable farm shop for a hardworking farmer that houses his/her heavy equipment.
A spacious storage building for the outdoorsman’s RV, boat, and ATV.
An equestrian’s dream horse barn equipped with an indoor riding arena.
The design flexibility of a post-frame building is mind-boggling.
For months, you’ve been mulling around the idea of building a pole barn. It’s a costly decision. A post-frame building is a large, permanent investment. Or at least, it should be permanent.
What is Pole Barn Structural Integrity?
Structural integrity refers to a pole barn’s ability to withstand anticipated structural loads without breaking. Any post-frame building, regardless of size and location, must be designed to resist vertical and lateral loads safely.
If you’re going to invest your money in a new structure, then you’ll have to make sure it’s engineered to handle various stresses. For instance, your pole barn will inevitably encounter inclement weather (e.g., rain, snow, and wind). How your post-frame building reacts to these situations will determine its lifetime.
Understanding the importance of pole barn structural integrity will help you:
- Make a well-informed buying decision
- Gain greater confidence and peace of mind
- Save money in the long run
Now, you’re probably wondering, “Where do I even begin?” We don’t expect you to be an expert in post-frame construction, let alone the structural integrity of a pole building.
In this article, we discuss the top five building components that will impact the structural integrity of your pole barn.
What is Pole Barn Structural Integrity?
Structural integrity refers to a pole barn’s ability to withstand anticipated structural loads without breaking. Any post-frame building, regardless of size and location, must be designed to resist vertical and lateral loads safely.
First, vertical loads act in the up-and-down direction. Popular applications of vertical loads include:
- Lofts
- Deck systems
- Second stories
- Snow on top of the building
- The weight of the building itself
Second, lateral loads act in a direction parallel to the ground, such as strong winds and seismic activity (earthquakes). These forces can work in any direction. Therefore, the pole barn must be designed to withstand loads, both parallel and perpendicular to any wall.
All structural loads must be able to pass from the areas in which the load is applied. This transfer of forces through the post-frame structure is called the load path. A continuous load path transfers all vertical and lateral loads from one building component to another until they reach the ground.
If the load path flows continuously without interruption, there will be no structural damage. However, one break in the course can cause damage.
One “weak link” is all it takes to compromise the structural integrity of your pole barn. Therefore, each building component must be strong enough to carry out these anticipated design loads.
It's crucial to keep structural integrity in mind should you decide to repair or renovate your pole barn. You'll want to speak with your post-frame builder to ensure any changes won't jeopardize your structure.
What Are the Top 5 Building Components of Pole Barn Structural Integrity?
Please note that your pole barn is only as strong as its weakest component. That’s why you must consider all areas of the building system before purchasing. Below, we list our top five building components that play a critical role in supporting the structural integrity of your pole barn.
1) Trusses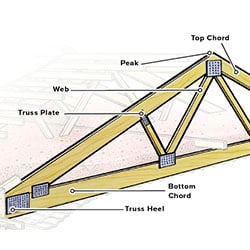
A truss is a rigid framework of members designed to support the roof. You’re probably familiar with its triangular shape. Trusses handle all the stresses received from the roof (via purlins and steel) and transfer those loads to the columns.
Having well-designed trusses is essential because if one fails, the others will follow pursuit. This domino effect results in building collapse.
To avoid truss failure, we recommend that you consider the following steps:
- Select a professional builder whose truss plant is certified by a third-party inspection service
- Check that your trusses are job-ordered and engineered for your pole barn
- Choose high-grade or Machine-Stress Rated (MSR) lumber (if applicable)
- Use heavy-duty steel plates to conjoin the lumber at critical points
It’s important to note that trusses are only one part of the overall building system. The entire post-frame structure must be designed to handle multiple stresses. You can have the most robust truss system, and your pole barn can still fail.
2) Fastening System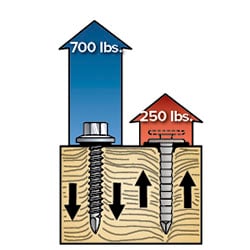
Next, the fastener is a restraint that holds something in place. The term “fastening system” refers to the type of fastener used and how/where it’s applied. In post-frame construction, fasteners are used for attaching wood to wood and steel to wood.
Also, the type of fastening system used to attach steel and wood plays a significant role in the structural integrity of your pole barn. Much of a post-frame building’s strength comes from the “diaphragm” created by the steel siding and roofing.
When comparing pole barn builders, you should pay close attention to the fastening system each one uses to attach the steel siding and roofing. It’s worth your while to evaluate different offerings before making a purchase.
After all, the fastening system a professional builder uses can have a dramatic effect on the structural integrity of your post-frame building. The right choice will provide a tight connection between wood and steel materials, ensuring a stronger structure that will still look good in the future.
When selecting a fastening system, we recommend using screws over nails. Why? Because the former has superior holding power compared to the latter (700 pounds vs. 250 pounds). But, that’s only part of the story.
Wood fibers tend to return to their original position when a screw or nail is driven inside. Nails push the wood fibers downward, while screws pull the wood fibers upward. As the fibers return to their original position, they push the nails out and pull the screws tighter.
When installing the fasteners into steel, post frame builders have two choices: the top of the rib or the flat area in between the ribs. Connecting in the flat area is a tighter, more secure construction method.
A firm, lasting grip maximizes seal effectiveness and strength. Look for a fastener that encapsulates the rubber washer (the last line of defense against leaks). If your washer is exposed to weather elements, it’ll degrade over time and become less effective. Then, those pesky leaks will create a rotten and weakened structure.
3) Foundation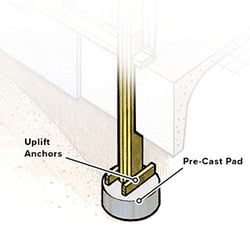
A foundation is a solid basis by which columns are supported. It should consist of properly installed and adequately sized footings to support the intended structure and applied loads.
Footings should extend below the exterior grade to be free of any frost action during the winter months. The ground should be well-compacted before footings are installed, or concrete is poured. Please check your local building codes for specific footing requirements.
Below, we provided three tips to consider when choosing a building foundation:
- The best foundations are either poured-in-place or precast concrete pads. These foundation types offer the solid, non-shifting, load-bearing support your pole barn needs.
- Look for a professional builder who offers crushed rock (e.g., gravel) as an option for backfilling the column hole. This type of rock provides more lateral and uplift resistance than soil.
- Avoid packaged, powdered concrete mix in the column holes as the basis for their foundation. Dry, powdered concrete mix requires ground moisture before it sets. Without adequate soil moisture, the concrete will remain loose and unstable.
4) Truss-to-Column Connections
A truss-to-column connection is a point at which the truss is fastened to a column. If properly designed and constructed, the truss-to-column connection works to strengthen and stabilize the truss.
These connections are crucial because they keep the load path continuous by transferring loads from the truss system, into the walls, and down to the ground.
What should you look for in truss-to-column connections? We recommend an integrated truss connection. This component is engineered so that the truss is interlocked with – not just attached to – the column.
Furthermore, an integrated truss connection allows for secure fastening from both sides of the column, doubling in strength and resisting loads effectively.
5) Roof Purlins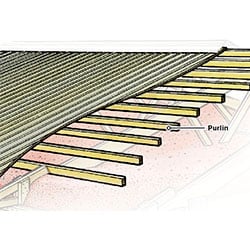
Lastly, roof purlins are horizontal members that span between the trusses to provide framing for sheathing material attachment. They’re responsible for resisting gravity and uplifting wind loads. In addition, purlins laterally brace rafters or the tops of trusses.
So, what should you look for in purlins? Well, you must select an appropriate lumber grade. We’ve all heard the phrase “bigger isn’t better.” A smaller-sized purlin made of high-grade lumber will carry more load than a larger purlin made of low-grade lumber.
Proper spacing is essential in carrying structural loads. Typically, purlins are spaced no more than 24’’ on center. If your post-frame builder uses screwed-down purlins or provides a fully engineered building design, then the purlin spacing may be increased.
Note: Purlin spacing and orientation depend on how far apart the trusses are spaced.
Moreover, we recommend overlapping purlins to create a stronger connection.
Request Your Structural Integrity e-Book to Get Started
By now, you should have greater peace of mind in regard to building performance, permeance, and safety. From the ground up, each building component plays a vital role in determining the structural integrity of your pole barn.
For more information about your building’s life cycle, you can download our FREE “Structural Integrity in Post Frame Construction” e-book. In the end, you’ll get the dream pole barn you’ve worked hard for and enjoy it well into the future.
Do you have more questions about pole barn structural integrity that are not covered in this article? If you need help designing and planning, please contact FBi Buildings at 800.552.2981 or click here to email us. If you are ready to get a price, click here to request a quote, and a member of our customer engagement team will help you determine the next steps of your project.