Posts | Building Tips | Site Preparation
How Do You Prepare Your Pole Barn for Concrete?
Angie joined FBi Buildings in 2012 and is now the Director of Marketing. She's an avid reader and enjoys outdoor leisure and cheering on her two daughters at their sporting events.
There are a lot of variables that go into place when you decide to build a pole barn. Some of them you may already know, some might come as a surprise to you. Deciding on what building materials to use might be easier than trying to figure out the appropriate set time for your concrete mix.
Regardless of what category you may fall under, it’s our job to make sure that you’re prepared for all the phases of post frame construction.
If I had to guess, your spare time might consist of designing your dream post frame building, skimming countless brochures, or scrolling through online galleries for inspiration. This process can be time-consuming or even overwhelming.
As mentioned above, there are multiple variables to consider from the ground up, such as:
Most importantly, you’ll need to select a type of pole barn flooring. After all, it’ll hold your personal property (e.g., machinery, products/services, and animals). There are several floor choices, ranging in style and price.
Before we dive deep into those options, you must establish a firm building pad (e.g., dirt/clay, sand and gravel, or stone). Aside from the foundation, this raised area serves as the basis for your post frame structure. A solid slab can be achieved through proper site preparation.
Before we dive too deep into discussing preparing your pole barn for concrete, it’s important to get a basic understanding of how proper site preparation will not only affect the pole barn construction but also the overall performance of your pole building.
What is Site Preparation?
Before your post frame builder can launch into construction, you need to make sure your job site is prepped.
Investing in site preparation will extend your pole barn’s lifetime and reduce total project costs.
The overarching goal is to ensure that your post frame project runs smoothly – on time and under budget.
For your convenience, we briefly detail the site prep steps regarding the building pad, which will affect your future flooring.
Where Should You Place Your Building Pad?
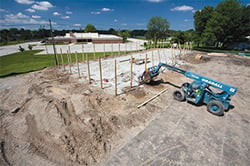
First, you must identify the exact position of your new pole barn. Please consider the following questions as you select a location:
- How will people and equipment move around your building and property?
- How will excess water drain away from your building? Where will it go?
- How will your new building line up in conjunction with existing structures or roadways?
- How much excavation does your proposed pad need to be level?
Your Project Sales Consultant (PSC) can draft an extensive site plan that will be communicated with the preferred excavator.
When Should You Construct Your Building Pad?
The beauty of post frame construction is its ability to build year-round. However, your excavator may disagree. Frozen ground (winter) and mud (spring) hinder pad preparation.
Prime excavation weather is in the summer and fall. These months are drier than others, which will keep your perimeter accessible for construction crews and equipment. Staying on schedule will minimize additional costs.
How Should You Structure Your Building Pad?
Building location? Check. Excavation date? Check. Now, it’s time to determine how you will structure your building pad.
The following factors will significantly influence the structural integrity of your new pole barn.
Elevation |
Crowning your pad from the center will direct water flow away from the structure. Proper grading will help achieve the desired elevation. |
Size |
Widening your pad on all four sides by 10’ minimizes erosion. Gradual tapering will occur. |
Compaction |
Stabilizes your pad and reduces damage caused by the common construction movement (less re-work). |
Fill Type |
Building with the correct granular fill is crucial. A layer of coarse stone over the soil base creates a capillary break and promotes drainage. |
Drainage |
Corrugated tile improves subsurface drainage. Connecting the downspouts to a tile system will direct water to strategic areas. |
Altogether, your post frame building must sit on a structurally-sound pad with good drainage.
How Do I Prepare My Pole Barn For Concrete?
Once your building pad is complete, we recommend keeping building use at the forefront. For instance, are you a(n):
- Hard-working farmer interested in storing your equipment?
- Entrepreneur interested in expanding your commercial business?
- Hobbyist interested in housing your antique tractor or classic car collection?
- Equine enthusiast interested in building your own stables and riding arena?
Did you answer “yes” to any of these questions? If so, do you know how to prepare your pole barn for concrete? If you answered no don’t worry...we have the perfect resource for you.
FBi's very own Al Schambach, P.E. and Terry Feldmann, P.E. of Maurer-Stutz, Inc. teamed up to compose an article featured in Frame Building News that will help you answer all of the questions you might have about the proper way to pour concrete.
Step 1: Determine the Purpose of the Building Slab
Sound design of a slab on grade begins with determining the intended use and performance criteria. How will the slab be used? What are the types and magnitude of the loads? Are there aesthetic requirements (e.g., is it acceptable to have random cracks or joints)?
For example, one might be designing a building slab that is subjected to vehicle traffic such as skid steer loaders, forklifts, trucks or tractors or some combination of these. In this case, the ability to handle repetitive loads and to transfer those loads across joints is a critical design criterion.
Alternatively, a slab may not have vehicle traffic but instead needs to be impermeable. Such is the case with the base of a storage tank for liquid manure. In some other slab uses (e.g., some farm shops or garages) the slab will receive limited vehicle traffic. The repetitions are likely not sufficient to control the slab thickness design, but other things—in-floor heat, surface finish including coatings, the slab slope or levelness—significantly influence the design.
Step 2: Proper Preparation
An adequate sub-grade for your planned slab on grade is one of the main keys to long-term performance. Sub-grade for concrete slabs is the natural ground, which is typically prepared by grading and compaction. For more critical slabs, an evaluation may involve a site-specific evaluation by a professional engineer.
Special considerations are required for problem soil such as highly expansive or compressive soils. Uniform soils that will provide reasonable support are desired. Except for highly organic soils and high-plasticity silts and clays such as those labeled CH or MH according to the Unified Soil Classification System.
Step 3: Establish Finish Floor Elevation (FF)
Another critical aspect of concrete flooring is establishing finish floor elevation (FF). This benchmark determines the location of your grade board and concrete depth.
Furthermore, the concrete depth (4’’ or 8’’) will dictate how high or low your grade board will sit. Miscommunication on this step can result in floor height and drainage issues. FF must be clearly marked before completing excavation and starting construction.
Concrete is one of the most popular floor selections in post frame construction.
It reduces the following annoyances associated with dirt, gravel, or stone floors:
- Dust build-up
- Excess moisture
- Inability to maintain a clean space
As a result, a concrete surface is often installed in farm shops, commercial businesses, hobby barns, and garages. Depending on the contractor, it's available in a wide variety of colors, finishes, and stamps.
If you plan on using concrete for livestock use, we recommend scoring the top layer with a broom or rake to eliminate any slips.
Additionally, you may want to invest in supplement flooring (e.g., rubber mats) to improve animal comfort. Standing on concrete alone for an extended period is detrimental to an animal’s health.
Are You Ready to Put Concrete in Your Pole Barn?
Ultimately, how you choose to design your pole barn is up to you. Our goal as one of the top post frame builders in the Midwest is to give you the information you need to know prior to construction starting.
Although FBi specializes in the building shell, we'd be more than happy to connect you to a reliable contractor within our network.
Do you have more questions that are not covered in this article? If you need help designing and planning, please contact FBi Buildings at 800.552.2981 or click here to email us. If you are ready to get a price, click here to request a quote and a member of our customer engagement team will help you determine the next steps of your project.