Building Maintenance | Posts | Videos | Building Tips | Repairs & Renovations
3 Tips to Help Prevent Pole Barn Rust
Angie joined FBi Buildings in 2012 and is now the Director of Marketing. She's an avid reader and enjoys outdoor leisure and cheering on her two daughters at their sporting events.
As you pull into the driveway, you can’t help but marvel at your 66’ x 120’ x 16’ farm shop. The overhead and sliding doors make it a breeze to move equipment around. The heated workshop is convenient when servicing heavy machinery during the slow winter months.
Fast forward to 40+ years worth of planting and harvesting seasons. Your post-frame building has undoubtedly worked just as hard as you.
Unfortunately, your farm shop is starting to show its age with a bit of rust on the metal panels. Red rust will expand if you don’t address this pole barn repair soon.
As you run your calloused fingers along the tarnish, you can’t help but wonder, “Why does my pole barn rust?”
Despite being the most common building material in post-frame construction, metal has one major flaw – rust. This article covers what causes pole barn rust and three tips to prevent it.
Why Does My Pole Barn Rust?
Rust is a form of iron oxide, which occurs when iron and oxygen cause corrosion. The main culprit behind a rusty metal panel is moisture buildup.
Although metal looks impenetrable to the naked eye, water molecules gain access through microscopic gaps. As a result, the steel sheet is weakened and becomes brittle or flaky.
Pole barn rust is inevitable, but there are a few preventative measures you can take to prolong corrosion:
- Use rust-resistant metal substrates
- Select building features that control condensation
- Perform routine pole barn maintenance
If the damage is already done, you can ask a post-frame builder to reskin your pole barn.
What is Pole Barn Rust?
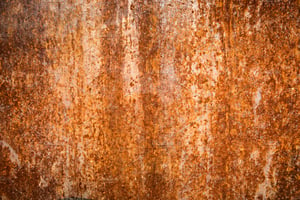
Rust is a form of iron oxide, which occurs when iron and oxygen cause corrosion. It appears in various colors, including the following hues:
- Red (most common)
- Brown
- Green
- Orange
- Yellow
The main culprit behind rust is moisture buildup. Although metal looks impenetrable to the naked eye, water molecules can gain access through microscopic gaps.
This infiltration is the first stage of corrosion. Exposing your post-frame building to carbon dioxide, salt, and sulfur dioxide will speed up the breakdown.
Rust causes the metal panels to expand, which stresses the pole barn. Meanwhile, the steel sheet is weakened and becomes brittle or flaky.
Introductory science class taught us that rust feeds off air and water. The metal layers beneath the tarnish will continue to oxidize.
3 Tips to Help Prevent Pole Barn Rust
As mentioned above, pole barn rust is inevitable. However, you can take these three preventative measures to postpone corrosion.
1) Use Rust-Resistant Metal Substrates
Popular rust-resistant metals used in post-frame construction include galvanized and galvalume steel.
First, galvanized steel is a substrate coated with a thin zinc layer (60, 90, or 100 ounces). This chemical element protects the metal panel from harsh components that cause corrosion.
Eventually, the zinc layer will fade. You’re probably thinking, “Wait a minute, isn’t that a bad thing?”
Remember, the zinc sacrificing itself in the event of a scratch stops the spread of rust.
Second, galvalume steel is glazed with zinc and aluminum by a continuous hot-dip process.
The alloy mixture consists of 45 percent zinc and 55 percent aluminum. It combines the protective properties of both chemical elements for a stronger coat.
Both metal substrates prevent pole barn rust, but galvalume outranks galvanized steel in terms of protection.
2) Consider Your Pole Barn Design
When you design your pole barn, you must consider adding building features that control moisture levels.
Pole barn condensation occurs when warm, moisture-laden air contacts a cooler surface. Since lower-temperature air cannot hold as much moisture as warm air, the excess humidity turns into water droplets.
Aside from rust, moisture buildup can cause the following damage to your post-frame building:
- Mold growth
- Lumber decay
- Poor human and animal health
- Discolored belongings stored inside
There are multiple ways to reduce pole barn condensation, starting at the beginning of your post-frame construction project. Below, we discuss five proactive factors that manage moisture buildup.
Site Preparation
Proper site preparation is the cornerstone of condensation control. The objective is to erect your post-frame building on a solid surface and establish the correct finish floor elevation (FFE).
Typically, the first step of site preparation is removing all humus and sod. If this organic isn’t removed, it’ll decompose and cause the concrete floor to settle or crack.
Fill should be applied one layer at a time and compacted to ensure a crowned surface. A layer of coarse stone over the soil base creates a capillary break to drain water away.
Poor groundwork can create capillary action and cause pole barn condensation. Fill material contains moisture (up to 15 pounds of water per cubic foot). It can take at least 6+ months to dry completely.
Although site preparation is an upfront cost, it’ll save you money (and headaches) in the long run.
Drainage
Now that your post-frame building is set high and dry, you should consider installing pole barn gutters and downspouts. Most post-frame builders already offer these standard building features.
Proper drainage manages water runoff from the metal roof and directs it away from the pole barn. Customers run their downspouts into tiles that feed into remote ditches or ponds.
Other Moisture Sources
Other factors that can increase the humidity inside your post-frame building include:
- Livestock (e.g., horses and manure)
- Non-vented furnaces
- Propane heaters
- Greenhouses
- Melting snow
- Water puddles around the building perimeter
As it cures, that water is released inside your pole barn interior. The release rate is 0.1 pounds of water per square foot per hour (in an enclosed, wind-free environment).
Pole Barn Ventilation
Next, pole barn ventilation goes a long way toward controlling condensation.
Overhangs with ridge vents at the metal roof peak pull warm, moist air out of your post-frame building and replace it with fresh, dry air.
Adding a cupola to your pole barn will allow trapped heat to escape through a fan and side vents. For a personalized touch, you can top it off with a weathervane.
Moreover, doors and windows provide ventilation, but that requires someone to open and close them as needed.
Mechanical ventilation controls air movement by using one or more ceiling fans. However, it isn’t commonly used for post-frame buildings because it increases initial operating costs.
Pole Barn Insulation & Roof Underlayment
Furthermore, wall insulation and roof underlayment are other ways to manage pole barn condensation. There are five types of wall and roof insulation that we recommend inside our post-frame buildings:
- Thermax insulation
- Vinyl back insulation
- OSB with felt paper
- MositureLOK
- Bubble wrap insulation (or radiant foil)
Editor’s Note: These building materials can condensate, so they should be used in addition to the other preventative measures discussed above.
3) Perform Routine Pole Barn Maintenance
Unless you’re going for the “rustic chic” look, performing routine pole barn maintenance is strongly urged to prevent or halt rust formation.
Pressure washing your post-frame building to remove dirt or debris will help with rust. If your pole barn is already showing aging signs, it’s crucial that you remove the rust.
You can treat tarnished areas with a traditional sander, wire brush, and chemical remover. The goal is to create a smooth metal surface. Then, don’t forget to remove the grime with soap and water.
Avoid strong solvents on painted metal panels. Apply primer to the stained spots. After 24 hours, you can paint over it with your desired pole barn color. Voila! Your metal siding looks good as new.
Will You Prevent Pole Barn Rust on Your Post-Frame Building?
Pole barn rust is a major disappointment, but you can install different building features to prolong the inevitable. Of course, performing routine maintenance plays a significant role too.
In some cases, the damage to your post-frame building is already done. Your pole barn looks like a weathered prop from a “Wild West” movie set.
But there’s no need to panic. Our 7+ and growing Repair & Renovation construction crews can restore your post-frame building to its pristine condition. Best of all, it does not matter who built the original structure!
For more information, we recommend downloading the Ultimate Guide to Pole Barn Repairs & Renovations.
Do you have more questions about pole barn rust that are not covered in this article? If you need help designing and planning, please contact FBi Buildings at 800.552.2981 or click here to email us. If you are ready to get a price, click here to request a quote, and a member of our customer engagement team will help you determine the next steps of your project.